Over the span of two years, the project delivered more than 20 million euros in cost savings and further significant CO2 reductions. The streamlined operations demonstrated that cost efficiency and sustainability can coexist effectively, setting a benchmark for the industry.
Watch the video to learn more:
A leading consumer durables manufacturer faced the challenge of enhancing procurement maturity while simultaneously cutting costs and reducing environmental impact. The company’s logistics operations could be optimized, with container fill rates below 70%, leading to excessive costs and higher CO2 emissions.
To address these issues, the manufacturer launched a joint project aimed at optimizing container utilization in Supply Chain. Through this initiative, they managed to increase the fill rate from below 70% to over 85%. This improvement resulted in significant outcomes:
- Financial Savings: Achieved 3 million euros in logistics cost savings.
- Environmental Impact: Reduced CO2 emissions by 400 tonnes.
Any questions? Then get in touch with our experts!
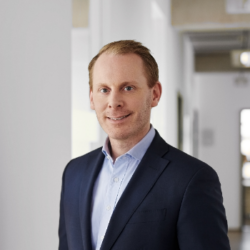
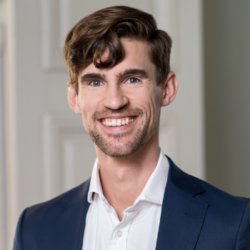