The steel industry is undergoing a green revolution, driven by technological breakthroughs and strategic collaborations, targeting cost-effective green steel production over the next 5 years. However, this is leading many procurement leaders to ask how they can benefit from the transition, secure supply and drive Scope 3 decarbonization across their supply chains? Find out in the following.
The global steel industry is gearing up for a transformative era focussed on decarbonization, driven by technological advancements, significant investments, and strategic collaboration. Key industry players, start-ups and governments are now joining forces to tackle the challenges that face this hard to abate sector, that represents approximately 7% of total global Co2 emissions.
Technological advancements are reshaping the steel industry
Within the next five years, several technologies are set to move the industry beyond providing incremental decarbonisation to reshape steel production and achieve commercial scale. Hydrogen-based Direct Reduced Iron (DRI) processes and Electric Arc Furnaces (EAF) are at the fore of the innovations that aim to significantly reduce carbon emissions in steelmaking and are soon to become a commercial reality. However, the use of Carbon Capture, Utilisation and Storage (CCUS) is also developing as a prospective technology that can be retrofitted into existing facilities (if its technical limitations relating to transport and storage can be overcome), with collaborations like the one between ArcelorMittal and Mitsubishi Heavy Industries Engineering working towards enhancing carbon capture techniques in the steel sector.
While the exact technology that will first emerge as commercially viable is unknown, the DRI-EAF pathway is expected to gain in importance over the foreseeable future, provided that it receives the necessary support from growth in high-grade iron ore pellet supply, scrap, and green H2 to achieve its full carbon-reduction potential.
Major European steel manufacturers like ArcelorMittal, are paving the way with pilot and large-scale facilities using hydrogen technology. These efforts are complemented by collaborations to secure input materials and enhance carbon capture techniques, fostering a holistic approach to decarbonisation.
Significant investments are being made that will make green steel a commercial reality
The global green steel production landscape is evolving, driven by key policies and market leaders. The Inflation Reduction Act (IRA) positions the USA as a leader in low-cost green hydrogen, while the EU’s Emissions Trading System (ETS) and Carbon Border Adjustment Mechanism (CBAM) will price carbon emissions by 2026, reshaping global steel economics.
In Europe, this decade offers a perfect opportunity for the steel industry to invest in EAFs as 74% of EU steel blast furnace capacity needs reinvestment by 2030. Failure to act could lock in polluting processes, endangering net zero goals.
China, the top steel producer, is investing in hydrogen technologies and EAFs to meet its 2060 carbon neutrality target. However, the ongoing downturn in the Chinese real estate sector, a key consumer of steel, is posing challenges. The construction slump has led to weakened steel demand, affecting price stability and profit margins, and potentially extending the asset lives of conventional blast furnace-basic oxygen furnaces (BF-BOF).
The ‘legacy’ BF-BOF method currently makes up 70% of global steel production, with an average cost of USD 490/t between 2015 and 2020. Cost estimates for 100% hydrogen-fuelled EAF are around USD 650/t for the first commercial-scale plants in 2025; 25% more expensive than BF-BOF.
However, EAF steel premiums are expected to fall across the USA, Europe, and China by 2030 due to incentives provided by the IRA and similar legislation that is accelerating their green hydrogen industries.
// Green steel is expected to be price competitive with legacy BF-BOF methods in the
United States and China by 2030 (USD/tonne)
Source: IEA
Leading companies are starting to assess how these additional costs can be passed on in many industry value chains with relatively limited price increases for the end customer. Although demand for green steel is difficult to calculate, BCG estimates European demand for green steel will reach 20-40 million tons by 2030.
However, in the face of growing demand, capacity constraints will likely present a challenge for companies and green steel volumes will be limited over the next 5-10 years due to constrained access to green (or blue) hydrogen at scale. Supply constraints are expected to be amplified as companies proactively compete to secure access to green steel and commit to long-term offtake agreements as production facilities come online.
What strategies can procurement use to drive cost-effective decarbonization with Green Steel?
For procurement leaders to guide their organizations through their decarbonization journey, while managing costs and ensuring supply, we recommend they prioritize the following actions:
To secure green steel supply, companies must engage strategically with suppliers. Building CEO/CPO level relationships and off-take agreements are essential. Developing Supplier Engagement Playbooks can help segment suppliers, identify negotiation levers, and craft strategic engagement programs. Establishing clear sustainability KPIs and financial incentives will also be crucial.
An integral component of a green transition is adopting low carbon sourcing strategies. Procurement and Sustainability teams will be increasingly tasked with the responsibility of conducting sourcing activities that actively reduce emissions through the exploration of alternative suppliers, products (such as green streel), or collaborative processes with suppliers (e.g. shared forecasts and dynamic inventory management practices that free up working capital to be invested back in the business).
While simultaneously achieving both cost reduction and improved sustainability performance is currently possible across some categories required for reducing Scope 3 emissions (e.g. transitioning to renewable energy), operational decision-making may need to be evolved to prioritise cost or sustainability trade-offs in many others (e.g. Steel and other raw materials).
Organisations that lead in developing this capability will need to give procurement and sustainability professionals an elevated seat at the table to define clear parameters for cost versus carbon prioritisation, gather necessary requirements from other functions (e.g. Engineering, Manufacturing, Construction, Commercial, etc.) and strategic business plans, to conduct RFPs that integrate sustainability criteria as a significant component of the evaluation.
To foster a true industry transformation and adoption of green steel, leading organisations will need to look beyond their immediate supply chains to consider developing Memorandums of Understanding (MoUs) within their broader ecosystem. This entails identifying and collaborating with key customers, government bodies, industry groups, and peers to drive a cohesive industry change.
Procurement teams can lead this charge by mapping out relevant value chain partners and developing opportunity lists that pinpoint areas where collaborative efforts can yield substantial commercial and decarbonisation improvements or reduce supply risks (e.g. securing critical raw materials such for scrap metal to reduce the CO₂ footprint by increasing circularity, high-quality iron ore pellets for use in DRI–EAF plants, green hydrogen and the required renewable electricity for DRI–EAF plants).
Green steel is on the horizon, and first movers will be best placed to take advantage
The green revolution in the steel industry requires a collaborative approach to procurement to secure raw materials and decarbonize supply chains. As green steel becomes a commercial reality, first movers will be best positioned to unlock commercial value and achieve sustainability goals. At INVERTO, we assist clients in navigating strategic and sustainable procurement, ensuring sustainability goals are embedded into supplier engagements and operational decision-making.
Authors: Tom Purnell, Theresa Schwämmlein
Get to know our experts
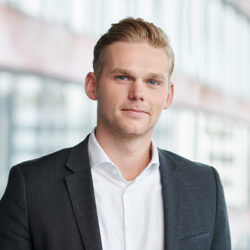
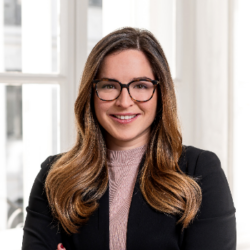